
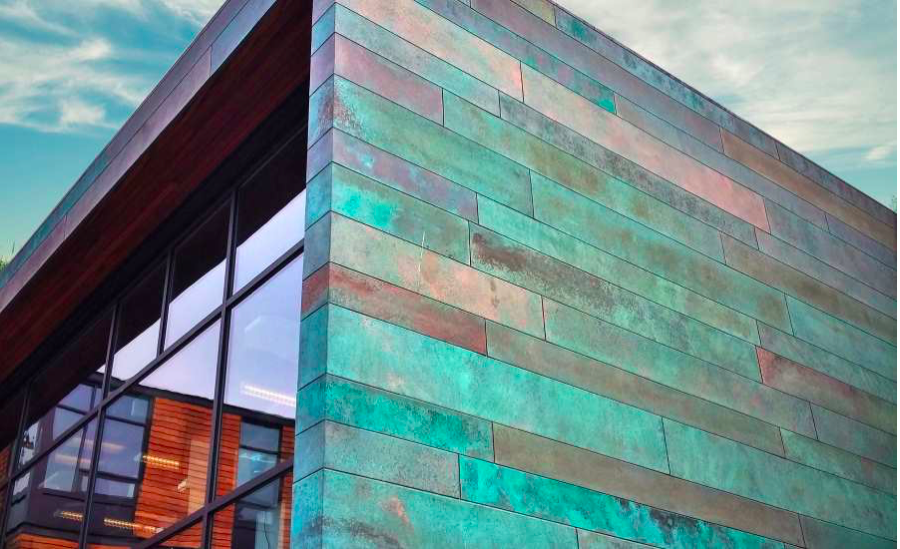
These products are often installed on battens using exposed fasteners. There are two additional factors to consider with stone-coated steel roofing. Basically, the homeowner is left with a rapidly failing roof often without specific warranty coverage for rust or granule loss. The field-repair solution these roofs consists of a bag of granules and a tube of glue to re-cover affected areas. That sets off a process of corrosion and rust causing the stones to separate from the steel panels in large patches. Once moisture gets through to the resin, it will eventually reach the steel. As the bonding resin breaks down, granules start to separate from the panels, allowing even greater water intrusion. Soaking a section of stone-coated roofing in warm water for as little as 20 seconds will soften the resin to the point of where the granules can be scraped off with a finger nail.Īs stone-coated products endure the various weather cycles, the bonding agent is continually broken down. The “glue” is a water-based acrylic resin that softens during various weather cycles. Stone coat technology evolved over time into a category of steel roofing products – essentially galvalume or galvanized base steel panels, with granules or stones glued to them. Unfortunately, widespread premature failure of these coatings occurred causing thousands of failed roofs in the 1960’s and 1970’s. The original bonding agent used between the panel and the small stones was basically road tar. At that time, a process was developed for bonding “stone” coatings to the surface of metal roofing after the metal panel was formed. Stone coated steel roofing goes back to 1950s Australia and New Zealand. While you may be attracted to the beauty of stone coated metal roofs, you should understand how these materials were developed and how they compare to other metal roofing options – especially if you’re after the best possible roofing solution available for your home. Recycled Content: Usually around 95% (mostly post-consumer).032” for standing seam and for some heavier tile profiles. Not as hail resistant, particularly in less-formed profiles.
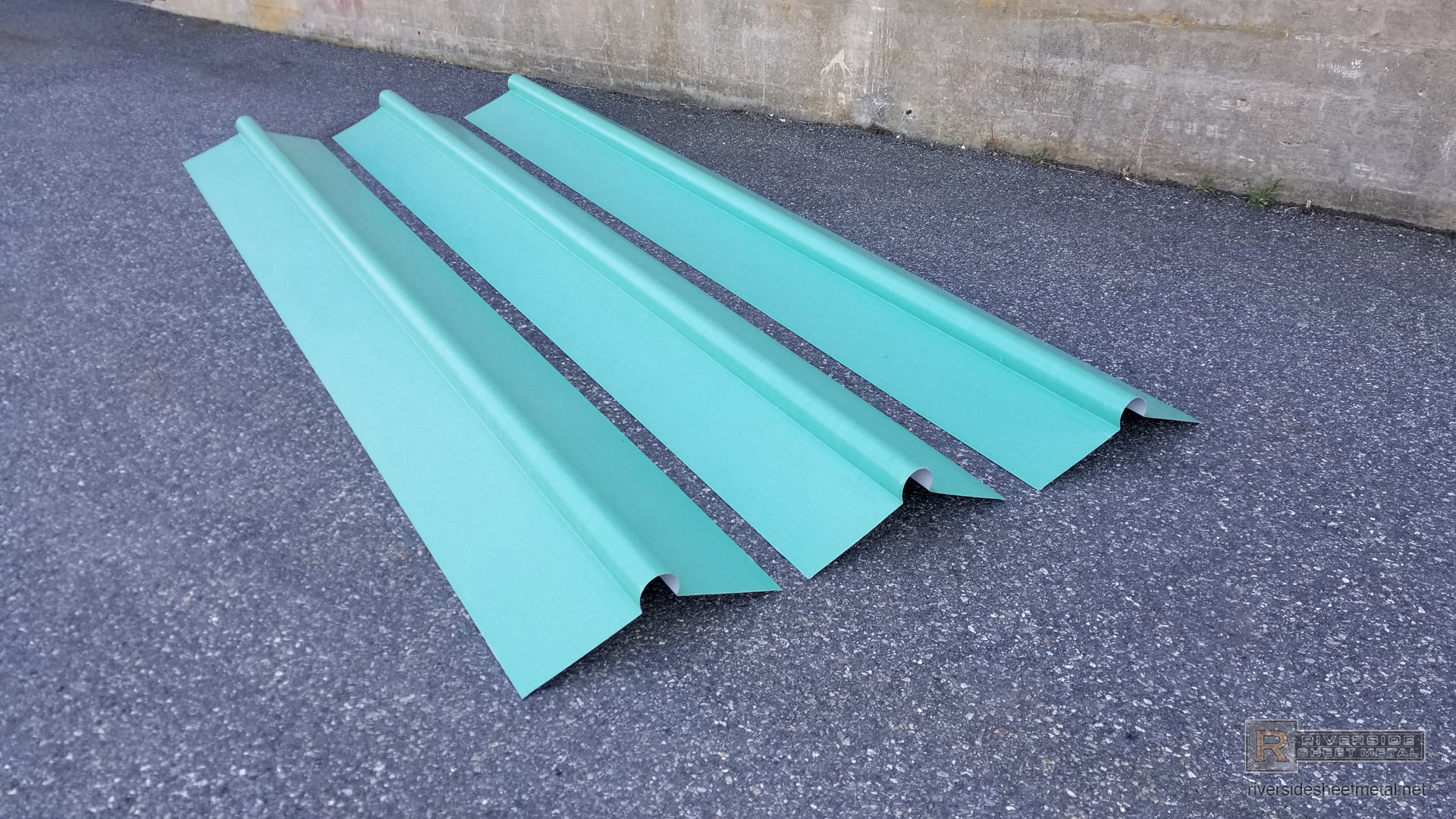

Disadvantages: More expensive than steel.Advantages: Lightweight, rust-free, attractive, energy-efficient.Many homeowners easily make the decision that residential aluminum roofing is the best choice they can make in terms of overall value. American Metal Roofs provides several aluminum product lines. One square of aluminum roofing (.019” thick) can use as many as 1,152 aluminum beverage cans-closing the recycling loop for the consumer. The recycled content of aluminum roofing will usually be 90 – 95%. Aluminum roofing is usually manufactured from a large percentage of recycled material, the majority of which is post-consumer material such as used beverage cans. In fact, more heavily formed products lend themselves very well to aluminum due to its high malleability and the fact that heavy forming adds additional structural strength. These days, virtually all aluminum roof systems are pre-painted, and aluminum can be found in just about any profile in which metal roofing is manufactured. Prior to that, aluminum had been considered a precious metal. It was around this time that processes to separate aluminum from bauxite and then manufacture building-grade aluminum alloys became efficient enough to make aluminum a viable option for the building industry. One of the first architectural aluminum applications was the cap on the Washington Monument in 1885. Aluminum’s propensity to resist rust gives it an extremely long lifespan. Aluminum will never rust, so it is an ideal metal for coastal applications and other areas where steel might be in danger. Lightweight, durable, and corrosion-resistant, aluminum is a great option for almost any residential metal roofing system, including standing seam, shake, shingle, tile, and slate profiles.

